―昨年を振り返って。
当社はOEM(相手先ブランドによる生産)でキッチン、理美容、美粧用からクラフト用まで、多種多様な約600種類のはさみを製造しています。コロナ禍ははさみも巣ごもり需要がありましたが、昨年は落ち着き、踊り場という状況でした。一方、鋼材や研削用の砥石(といし)の価格高騰に加え、賃金の上昇が課題となっており、発注元に理解をいただきながら対応を進めています。昨年は電気使用量や購入電力を削減するため、工場5棟のうち2棟の屋根に太陽光パネルを設置して、8月から稼働しました。平日は自家消費して電気使用量の約4割を賄い、休業日に発電した余剰電力は売電し、利益の確保に努めています。近年は自社の生産設備用にメーカーと開発した特殊潤滑油の販路開拓にも注力しています。
―今年力を入れることは。
職人が高齢化する一方、急速に進む少子化で地方の中小企業は人材採用がますます厳しくなっています。十数年前から取り組んでいますが、今年も製造工程の自動化は継続します。形状が複雑なはさみの背の研削工程の自動化に着手したいと考えています。最後の切れ味を確認する検査は、職人の技が不可欠ですが、人工知能(AI)による画像認識で傷や汚れを確認するシステムもできないかと思っています。
―岐阜大と協同組合岐阜関刃物会館との共同研究が昨秋、本格始動した。
岐阜大に開設された関の刃物サステナブル技術革新拠点と刃物関連事業者が10年かけて、品質管理、機械化・自動化、新素材の開発の三つのテーマで共同研究と人材育成を進めます。県関刃物産業連合会会長として計画を進めてきた事業で、関の刃物産業全体が将来に希望を持てる成果が出ることを期待しています。当社も新素材のテーマで参画しており、関の刃物業界が享受できるようメード・イン・関の素材の開発を目指したいと思います。
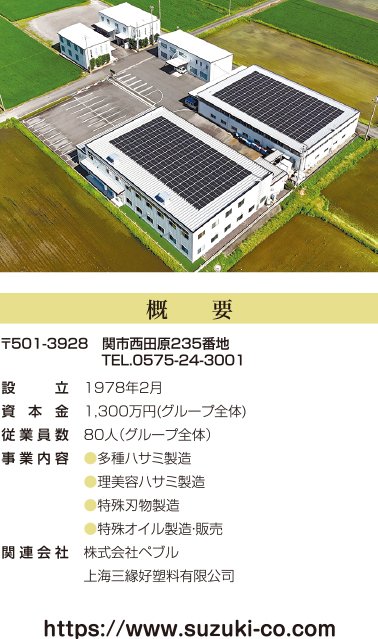